ویژگی های ساختاری و مکانیکی
با بوجود آمدن پیشرفت های اخیر در زمینه ی مهندسی سطح و تکنولوژی های
رسوب دهی، طراحی و تولید پوشش های کامپوزیتی و نانو ساختار نسبتا آسان شده
است. برخی از متداول ترین طراحی های انجام شده برای تولید پوشش های نانو
ساختار شامل تولید معماری های چند لایه و نانو کامپوزیتی مانند آنهایی است
که در شکل 1 و 3 بخش اول این مقاله نشان داده شده است. در مورد پوشش های
چند لایه، ضخامت لایه ممکن است از چند اتم تا چند آنگسترم یا چند نانومتر
تغییر کند. برخی از این پوشش ها، پوشش های ابر شبکه نامیده می شوند( شکل1).
یک چنین پوشش هایی ممکن است ابر سختی و تافنس بالایی از خود نشان دهند و
علاوه بر آن، پایداری حرارتی این پوشش ها نیز ممکن است بالا باشد. سایر
استراتژی های طراحی می توانند بر پایه ی لایه های بسیار نازک، مدرج نمودن
در مقیاس نانو یا میکرو، لایه های در هم گسیخته یا غیر مداوم و ... ایجاد
شوند. موفقیت در حصول ساختارهای لایه ای با دقت بالا، به چندین فاکتور
بستگی دارد. این فاکتورها شامل انتخاب و کنترل مؤثر پارامترها در طی
فرایند، می شود. این پارامترهای ممکن است نقشی مهم در نفوذ سطحی و بالک اتم
های ناخالصی ایفا کنند و همچنین بر روی موبیلیته ی اتم های اضافه شده به
سطح در طی رسوب دهی، جوانه زنی و فرایند های رشد نیز تأثیر دارند و از این
رو این پارامترها بر روی یکنواختی و پوشانندگی مواد زیرلایه نیز مؤثرند.
یکی دیگر از استراتژی های متداول در تولید پوشش های نانو ساختار، تولید
فیلم های نانو ساختار با استفاده از سیستم های CVD و PVD هیبریدی است. یک
پوشش نانوکامپوزیتی نمونه وار از فازهای نانوکریستالی تشکیل شده است که
بوسیله ی فازهای کربنی، سرامیکی و یا فلزی در آغوش گرفته شده است. فازهای
آمورف و فلزی در حجم های بسیار اندک بوجود می آیند و به گونه ای انتخاب می
شوند که چسبندگی خوبی با فازهای کریستالی سخت داشته باشند. این مسئله نیز
محتمل است که بیش از یک فاز کریستالی در فاز زمینه ای آمورف داشته باشیم.
استحکام تسلیم یک چنین فیلم های نانوکامپوزیتی ممکن است نسبت به استحکام
تسلیم مشاهده شده برای اشکال کریستالی بالک از این مواد، متفاوت باشد. برخی
از فاکتورهای عمده که می تواند بر ویژگی های مکانیکی و تریبولوژیکی یک
چنین پوشش هایی اثر گذار باشد، اندازه، شکل و جهت گیری نانو دانه ها، مساحت
سطح و ضخامت فاز مرزدانه ای، تنش های باقیمانده و گرادیان تنش در عرض پوشش
می باشد.
در سال های اخیر، چند مدل تئوری برای ویژگی های فوق العاده ی فیلم های
نانو ساختار و کامپوزیتی، پیشنهاد شده است( مخصوصا برای سختی و مدول
الاستیک). در یکی از این تئوری ها، Koehler پیشنهاد کرده است که افزایش
چشمگیر در سختی پوشش های نانو ساختار ممکن است تا حد زیادی به خاطر این
موضوع باشد که در این مواد نابجایی ها به طور الاستیک از مرزدانه ها، دفع
می شوند و از این رو، از ایجاد تغییر شکل پلاستیک ممانعت می شود. یکی دیگر
از تئوری ها پیشنهاد می کند، رابطه ی هال پچ مهم ترین دلیل برای ابر سختی
در پوشش های نانو ساختار می باشد. با توجه به رابطه ی هال پچ (
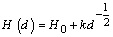
) ، استحکام تسلیم(

) یک جامد پلی کریستال با اندازه ی متوسط دانه های آن مرتبط است( در اینجا

و k ثابت های خاص ماده هستند). عموما، وجود دانه های ریزتر موجب می شود تا
ماده سخت تر باشد. در مواد بالک یا کامپوزیت ها، این رابطه ممکن است تا
اندازه ی دانه ی 0.01 میکرون صدق کند، اما در کمتر از این مقدار از اندازه،
سختی ممکن است کاهش یابد( عمدتا به دلیل افزایش لغزش مرزدانه ها). اگر
مرزدانه های یک ماده ی کامپوزیتی یا یک پوشش به نحوه ای طراحی شوند که سخت
باشند، بنابراین مقدار سختی این ماده بالا می رود. این مسئله حتی در اندازه
دانه های کمتر از 0.01 میکرون نیز رخ می دهد. جدول 1 ترکیب شیمیایی و
وِیژگی های مکانیکی برخی از پوشش های نانو کامپوزیتی که اخیرا در گروه های
تحقیقاتی مختلف، تولید شده است، نشان داده شده است.
در حال حاضر، چند فیلم نانو ساختار و نانو کامپوزیتی وجود دارد که این
فیلم ها، سختی هایی در حدود 40 GPa ایجاد می کنند. این پوشش ها، پوشش های
ابرسخت نامیده می شوند. در این مورد، دانه ها در اندازه ی نانومتری قرار
دارند( 3 تا 5 نانومتر) و مرزدانه ها در این مواد بسیار نازک هستند( در حد
یک یا دو اتم هستند) و غیر قابل امتزاج هستند اما این فازها به طور محکم به
هم متصل شده اند. یک اثر مشابه( یا همان اثر ابر سختی) می تواند بوسیله ی
تولید فیلم های نانو کامپوزیتی دارای دو یا چند فاز کریستالی ایجاد شود.
این فازها ممکن است در مرزدانه ها، به طور محکم به هم پیوند خورده باشند به
نحوی که در این مواد لغزش مرزدانه ها بسیار مشکل است.
ویژگی سختی غیر عادی پوشش های نانو کامپوزیتی با استفاده از قوانین مخلوط
شوندگی ساده قابل دستیابی نمی باشد. برای مثال، برخی از پوشش های
نانوکامپوزیتی که اخیرا توسعه یافته اند( مانند

دارای سختی هایی بالاتر از 40 GPa می باشد. اگر هر فازی که این پوشش های
کامپوزیتی را تشکیل داده است را در نظر بگیریم، این واضح است که سختی این
کامپوزیت باید کمتر از این مقادیر باشد. به هر حال، این اثبات شده است که
این پوشش ها دارای سختی دو تا سه برابر بزرگتر نسبت به فازهایی هستند که
این کامپوزیت ها را تشکیل داده اند. عموما، این تصدیق شده است که با انتخاب
و استفاده ی مناسب از فازهای سرامیکی و فلزی، این احتمال وجود دارد که
فیلم های کامپوزیتی بسیار نرم تولید نمود که مقادیر سختی آنها کمتر از 10
GPa و یا بیشتر از 50 GPa می باشد. به طور خلاصه باید گفت که پوشش های نانو
کامپوزیتی می تواند به گونه ای طراحی شوند که ویژگی های مکانیکی آنها را
بتوان تنظیم نمود.
علاوه بر ابر سختی، تافنس شکست یک پوشش بسیار مهم است؛ مخصوصا برای
کاربردهای تریبولوژیکی که در آنها نیروهای برشی و نرمال بالایی وجود دارد.
سختی به تنهایی ممکن نیست میزان مناسبی از محافظت را در برابر تماس های
لغزشی در کاربردهای ماشین کاری ایجاد کند. برخی اوقات، میزان بالایی از تنش
های داخلی در داخل فیلم ها ممکن است تا حدی دلیلی برای ایجاد ابر سختی
هایی باشد که در این پوشش ها مشاهده می شود. و یک چنین وضعیتی ممکن است
مقاومت به سایش و خستگی یک چنین پوشش هایی را تعیین کند. مطالعات تجربی
اخیر تأیید نموده است که پوشش های نانو ساختار و کامپوزیتی دارای تافنس
شکست نسبتا بالایی هستند. این پیشنهاد شده است که مرفولوژی دانه های نانو
سایز می تواند یک وضعیت ایده آل برای ایجاد مقاومت در برابر شروع ترک،
فراهم آورد. حتی اگر یک ترک در داخل دانه شروع شود، مرزدانه های مقاوم می
توانند از رشد این ترک جلوگیری کنند. در کل، ابر سختی و تافنس به طور کامل
در پوشش های کامپوزیتی و نانوساختار قابل حصول می باشند. این کار با ایجاد
مرزدانه های با استحکام بالا، کنترل انرژی سطحی و سطح مشترک نانو دانه ها،
ایجاد بافت و تنش باقیمانده در فیلم، ایجاد می شود.
در سال های اخیر، محققین بسیاری بر روی طراحی یک پوشش نانوکامپوزیتی جدید
تمرکز کرده اند که این پوشش دارای سختی در حد الماس هستند. برای پاسخگویی
به این درخواست، چندین سیستم پیچیده ی پوششی که دارای دو یا تعداد بیشتر
فاز هستند، مورد بررسی قرار گرفته است. بیشتر نیتریدهای دیرگداز با آمیختگی
اندک و یا عدم آمیختگی این وضعیت را ارضا می کند. یک چنین سیستم پوششی
اخیرا بوسیله ی Veprek طراحی شده است. این سیستم پوششی از فازهای TiN نانو
کریستالی قرار گرفته در زمینه ای آمورف از

و فاز نانوکریستالی

تشکیل
شده است. مقدار سختی گزارش شده برای این پوشش بیشتر از 100 GPa می باشد.
چند سیستم دیگر( مانند (Ti,Al)N و VN) که دارای سختی بالایی هستند نیز در
واحدهای PVD و CVD طراحی و تولید شده اند.
علاوه بر سختی و تافنس بالا، چسبندگی قوی میان فیلم و زیرلایه مهم ترین
پیش نیاز برای کاربردهای تریبولوژیکی و مکانیکی است. اگر چسبندگی ضعیف
باشد، پوشش به سرعت تحت نیروهای برشی و نرمال، جدا می شود( این نیروها در
سطح مشترک فیلم- زیرلایه و به دلیل اختلاط شیمیایی و فیزیکی نامناسب، یا
قفل شوندگی مکانیکی در سطح مشترک ایجاد می شود). در بیشتر کاربردهای
تریبولوژیکی، چسبندگی عمر عملیاتی فیلم و ظرفیت تحمل بار را تعیین می کند و
از این رو این چسبندگی میزان تأثیر این پوشش ها در این کاربردها را تعیین
می کند. با بوجود آمدن پیشرفت های اخیر در این زمینه، این ممکن است که
بتوان پیوند بسیار قوی میان پوشش نازک و زیرلایه ایجاد کنیم. بوسیله ی PVD
قوسی و کندوپاش مگنترونی پالسی توان بالا، می تواند یک سطح تمیز( از لحاظ
اتمی) ایجاد نمود و سطح بالایی از نفوذ یا اختلاط را در سطح مشترک زیرلایه و
پوشش پدید آورد. با این کار این اطمینان حاصل می شود که پیوند قوی در میان
زیرلایه و پوشش ایجاد شده است. به هر حال، برخی استثناها وجود دارد.
علارغم ابر سختی و ویژگی های تریبولوژیکی جذاب، نیترید بور کیوبیک یا برخی
پوشش های بر پایه ی B- C- N هنوز هم از چسبندگی ضعیف و تنش های داخلی بالا
رنج می برند. بنابراین این پوشش ها هم اکنون به طور گسترده در کاربردهای
تجاری مورد استفاده قرار نمی گیرند.
در بیشتر کاربردهای تریبولوژیکی، شرایط عملیاتی به صورت دمای بالا یا
محیط های خورنده نمود دارند. بنابراین، این انتظار وجود دارد که پوشش های
تریبولوژیکی به صورت شیمیایی و ساختاری با تغییرات دمایی محیطی و دمایی
مقاوم هستند. تحت تأثیر حرکت های لغزشی مداوم، پوشش های نانوکامپوزیتی و
نانو ساختار ممکن است متحمل برخی تغییرات شیمیایی یا ساختاری شوند. این
تغییرات در حقیقت منجر به تخریب تدریجی ویژگی های تریبولوژیکی و مکانیکی
این پوشش ها می شود. در طی استفاده از این پوشش ها تحت محیط های خورنده یا
هوای آزاد، این انتظار وجود دارد که برخی تغییرات شیمیایی در پوشش های خاص
ایجاد شود( مخصوصا در نزدیکی سطوح لغزشی). با وجود اینکه، برخی اوقات این
پوشش ها از لحاظ شیمیایی پایدار هستند، این پوشش ها ممکن است اکسید شوند.
با افزایش میل در زمینه ی ماشین کاری خشک و افزایش اشتیاق برای انجام
عملیات های شکل دهی فلزات در دماهای بالا، پایداری شیمیایی و حرارتی این
سیستم های پوششی مهم تر از قبل شده است. این به نظر می رسد که دپ کردن این
مواد با Al، Y، Ce و ... رفتار اکسیداسیون این پوشش ها بهبود می یابد و از
این رو عمر مفید ابزارها و قالب های مورد استفاده در این کاربردها، افزایش
می یابد.
تریبولوژی فیلم های نانوساختار و کامپوزیتی
اگر چه جنبه ی فیزیکی، شیمیایی و مکانیکی تماس های لغزشی میان سطوح
تریبولوژیکی به درستی فهمیده نشده است، تحقیقات پیشین نشان داده است که
پوشش های نازک می توانند به طور مؤثر هم خواص سایشی و هم خواص اصطکاکی این
سطوح را بهبود دهند. امروزه، بیشتر ابزارآلات و قالب های مورد استفاده در
عملیات های تولید، به طور روتین با فیلم های محافظت کننده، محافظت می شوند.
با انجام پیشرفت های اخیر در زمینه ی تکنولوژی های PVD و CVD، چند سیستم
پوششی جدید توسعه یافته اند و از آنها برای فایق آمدن بر اصطکاک، در بسیاری
از کاربردهای صنعتی مورد استفاده قرار می گیرد. مخصوصا استفاده از پوشش
های کامپوزیتی و نانو ساختار به طور فزاینده ای متداول شده است.
همانگونه که قبلا اشاره شده است، اگر یک پوشش تریبولوژیکی برای یک کاربرد
معین، مفید باشد، این پوشش باید نیازمندی های مهمی را برطرف کند. این
نیازمندی ها عبارتند از چسبندگی قوی، سختی مکانیکی و تافنس بالا، پایداری
حرارتی و شیمیایی پایدار، یکنواختی در ضخامت، سطح نهایی یکنواخت، اصطکاک کم
و ... . از لحاظ ساختاری، این پوشش ها همچنین دارای مورفولوژی های پر
دانسیته ای هستند( یعنی هیچ تخلخل و یا حفره ی بازی در مرزدانه ها وجود
ندارد). پوشش های با ساختار ستونی متخلخل با سرعت بیشتری در کاربردهای
تریبولوژیکی سایش پیدا می کنند. نتیجه ی نوسان یا خمیدگی دانه های ستونی با
چسبندگی داخلی ضعیف در طی عملیات های ماشین کاری یا در طی عملیات های
لغزشی، ایجاد میکرو ترک ها و بوجود آمدن سایش است. بنابراین، ایجاد پیوند
چسبندگی قوی در میان دانه های یک پوشش بسیار مهم می باشد. یکنواختگی ضخامت
پوشش همچنین برای بهبود کارایی پوشش مهم می باشد. وقتی تمام این نیازمندی
ها برطرف شود، پوشش های تریبولوژیکی می تواند اثر مثبتی بر روی یک کاربرد
معین داشته باشند. مخصوصا این پوشش ها می توانند عمر و کارایی این اجزا را
افزایش دهد.
وقتی از پوشش های نانو ساختار بر روی سطوح لغزشی استفاده می شود، این
پوشش ها میزان مشابهی از فشار تماسی را نسبت به پوشش های معمولی دریافت می
کنند. اگر در وضعیتی که در آن مکانیزم های سایش موجب پدید آمدن میکروترک و
تغییر شکل پلاستیک شود، یک چنین پوشش هایی می توانند در برابر شروع ترک
مقاومت کنند. علت این موضوع این است که تافنس شکست این پوشش ها بالاست. اگر
این پوشش ها تحت بارگذاری سنگین در جهت قائم قرار گیرند، آنها ممکن است به
سهولت پوشش های معمولی شکسته نشوند. همانگونه که مشخص شده است، بیشتر پوشش
های معمولی به شدت آنیزوتروپ هستند و از این رو مستعد تغییر شکل و یا شکست
هستند. به هر حال، در مورد پوشش های نانو ساختار، دانه ها خیلی ریز هستند و
مورفولوژی به طور ضروری آنیزوتروپ یا ستونی نیستند. شکل 2 مورفولوژی سطح
مقطع یک فیلم MoN معمولی را با مورفولوژی ستونی و یک فیلم Cu/MoN ابر سخت
را با مرفولوژی خاص را نشان می دهد. توجه کنید که ترک های اضافی از سطح
بریده شده، دور هستند و در جهت دانه های ستونی MoN معمولی قرار گرفته اند؛
اما یک چنین ترک هایی در پوشش های cu/MoN نانو کامپوزیتی وجود ندارد.
اندازه ی دانه ی متوسط فیلم های نانو کریستالی در گستره ای است که برای
آغاز و گسترش ترک مناسب نمی باشد. به عبارت دیگر، معیار گریفیس برای رشد
ترک در پوشش های نانوساختار و کامپوزیتی به سختی ارضا می شود. بنابراین این
عقلانی است که استدلال کنیم که یکی از دلایل اصلی اینکه پوشش ه ای نانو
ساختار دارای ویژگی های سایشی متفاوت هستند، این است که آنها به طور مناسب
تری می توانند از ایجاد و گسترش ترک جلوگیری کنند.
سختی و سفتی فوق العاده ی فیلم های نانو ساختار و کامپوزیتی این اطمینان
را ایجاد می کند که در طی وضعیت های لغزش تریبولوژیکی، نواحی حقیقی تماس
بین سطوح بسیار کوچک است. پوشش های تولید شده در حالت ابر شبکه یا چند
لایه، می تواند اساسا ظرفیت تحمل بار سطوح لعزشی را افزایش دهد. عموما وقتی
سطح تماس اندک با خنثی بودن شیمیایی یا پایداری این پوشش ها ترکیب می شود،
این مسئله منجر به کاهش اصطکاک می شود. وقتی انتخاب فازی به طور مناسب
انجام شود، یکی از فازها در فیلم نانو کامپوزیتی می تواند نیروی برشی را
کاهش دهد و از این روش اصطکاک در طی تماس های لغزشی کاهش می یابد. پوشش های
نانو کامپوزیتی و چند لایه می توانند همچنین به گونه ای طراحی شوند که
وقتی آنها را در کاربردهای لغزشی مورد استفاده قرار می دهیم، آنها خاصیت
خود روان سازی ایجاد کنند و بنابراین اصطکاک کوچک تری ایجاد کنند. وقتی
پوشش های Sn/MoN را با سطوح فولادی بدون پوشش مقایسه می کنیم، این پوشش های
ضریب اصطکاک کمتری ایجاد می کنند( شکل 3). این ممکن است که کاهش در اصطکاک
یک چنین پوشش هایی به دلیل استحکام برشی پایین فاز Sn در ساختار
نانوکامپوزیتی ایجاد گردد. Sn ممکن است همچنین با افزودنی های موجود در
روغن های روان ساز واکنش دهد و فیلم مرزی با نیروی برشی پایین ایجاد کنند.
پوشش های نانوکامپوزیتی خود روان ساز
تولید و استفاده از مواد و پوشش های کامپوزیتی خود روان ساز برای
کاربردهای تریبولوژیکی در این بخش مورد بررسی قرار می گیرد. برای سال های
متمادی، کامپوزیت های زمینه فلزی، سرامیکی و پلیمری با قابلیت خود روان
سازی به طور موفقیت آمیز تولید شده اند و برای فایق آمدن بر اصطکاک و سایش
در بسیاری از کاربردهای مکانیکی مورد استفاده قرار گرفته اند. پوشش های
کامپوزیتی ضخیم( 0.1 تا 0.2 میلی متر) و خود روان ساز که به روش پلاسما
اسپری تولید می شوند، بر روی پوشش های لغزشی اجزای مهندسی مورد اعمال شده
اند. این پوشش ها مخصوصا در دماهای بالا بر اصطکاک و سایش غلبه می کنند.
چند پوشش کامپوزیتی دیگر که دارای گرافیت، مولیبدن دی سولفید و نیترید بور
هگزاگونال( HBN) هستند نیز از طریق روش های پلاسما اسپری یا روش
الکتروپلیتینگ تولید شده اند. این پوشش ها دارای ویژگی های تریبولوژیکی و
مکانیکی خوبی هستند. توسعه و استفاده از پوشش های نانو ساختار و نانو
کامپوزیتی نازک ضروری است. نانو آلیاژسازی پوشش های نازک با فلزات خاص ممکن
است همچنین منجر به ایجاد ویژگی های تریبولوژیکی فوق العاده برای
کاربردهای تریبولوژیکی شود.
در گذشته، یک سری از عناصر آلیاژی به پوشش های معمولی اضافه شده اند که
این افزایش موجب بهبود ویژگی های مکانیکی و قابلیت های محیط زیستی این پوشش
ها می شود. مثال اولیه از این فیلم ها، فیلم های

هستند
که دارای کاربردهای فراوانی در هوافضا و برخی کاربردهای دیگر هستند. برخی
از عناصر یا ترکیبات آلیاژی که در این پوشش ها مورد استفاده قرار می گیرند،
عبارتند از Au، Ni، Ti، Pb، C، TIN، PbO،

، و ... . مطالعات تریبولوژیک نشان داده است که وقتی آلیاژسازی به طور
مناسب انجام شود، این گرایان آلیاژی می تواند به طور مناسبی ویژگی های فیلم
های

با Pb، Ti، Ni، Fe، Au و

منجر به آمورف شدن ساختار یا نانو کریستالی فیلم می شود که در حقیقت این
مسئله نیز اصطکاک را کاهش داده و عمر مفید قطعه را بالا می برد. در سال های
اخیر، الکترولس نیکل، کروم و پوشش های فسفری نیکل دار که دارای مقادیر
اندکی گرافیت نانو مقیاس،

، PTFE و ذرات الماسی هستند، توسعه یافته اند. توسعه ی این روش ها منجر به
تولید پوشش های نسبتا ضخیم با خواص خود روان سازی شده است.
از دهه ی 1990 تاکنون، علاقه ها در این این گونه از پوشش ها، به سمت
تولید پوشش های نانوساختار و کامپوزیتی خود روان ساز حرکت کرده است. این
احساس می شود که با طراحی و ساخت یک چنین پوشش هایی، کارایی تریبولوژیک این
پوشش ها به طور قابل توجهی افزایش یافته است. از لحاظ مفهومی، این روش
مشابه روش های معمولی مورد استفاده در تولید مواد و پوشش های کامپوزیتی
بالک خود روان ساز است که در بالا معرفی شده اند. علاوه بر این، از لحاظ
ساختاری، دانه های منفرد که یک چنین پوشش هایی را در تشکیل می دهند، در
مقیاس نانو قرار گرفته اند و یا به طور هموژن از لایه های متوالی تشکیل شده
اند. از لحاظ شیمیایی، یک چنین پوشش هایی ممکن است شامل فازهای نانو مقیاس
سخت و نرم باشند که این فازها موجب پدید آمدن تافنس بالا، قابلیت تحمل بار
بالا، اصطکاک کمتر و مقاومت به سایش بیشتر در بخش های لغزشی می گردد. در
یک چنین سیستم های پوششی، کاربیدهای سخت و فازهای کربنی ممکن است سختی
بالایی ایجاد کنند و از این رو مقاومت به سایش در این پوشش ها بالاست. این
در حالی است که در این پوشش ها، فاز نرم تر اصطکاک را کاهش داده و قابلیت
تحکل بار را افزایش می دهد.
فازهای نرم روان کننده در فیلم های نانو کامپوزیتی خود روان ساز ممکن است
از جنس گرافیت، HBN و سولفید های فلزات انتقالی باشد. این مواد روان ساز
ویژگی روانسازی خود را مدیون ساختار کریستالی لایه ای خود هستند. همانگونه
که در شکل 4 نشان داده شده است، ساختار کریستالی این جامدات به نحوی است که
در حالی که اتم ها در یک لایه ی یکسان قرار دارند، به سختی به هم پیوند
داده اند. این ساختار لایه ای مجزاست و نیروهای موجود در بین لایه ها از
جنس نیروهای واندروالس هستند. وقتی این مواد در بین بخش های لغزنده قرار می
گیرند، این لایه ها می توانند به طور موازی با جهت حرکت نسبی حرکت کنند و
از این رو اصطکاک را کاهش می دهند. این مواد به طور گسترده در کاربردهای
تریبولوژیکی مورد استفاده قرار می گیرند. در بین سولفیدهای،

و

به طور گسترده به صورت پوشش های نازک و یا ضخیم برای اهداف روان سازی جامد
در کاربردهای هوافضا مورد استفاده قرار می گیرند. در گازهای خنثی یا محیط
های شبه فضایی، این مواد می توانند ضرایب اصطکاک 0.01 را ایجاد کنند. به هر
حال، در دماهای بالا و در محیط های مرطوب و اکسیدی، اصطکاک این مواد ممکن
است بیشتر شود و یا نوسان داشته باشد.
مواد سولفیدی اشاره شده در بالا به عنوان مواد خود روان ساز در پوشش های
تریبولوژیک نانو لایه یا چند عملکردی مورد استفاده قرار می گیرند. یکی از
فیلم های نانو لایه ای بر اساس سیستم

و Ti تولید می شوند. این پوشش با استفاده از روش پوشش دهی کندوپاش یونی-
مگنترونی غیر تعادلی( میدان نزدیک) تولید شده است. شکل 5 رفتار اصطکاکی یک
چنین فیلمی را در محیط هوای مرطوب و نیتروژن خشک نشان می دهد. این فیلم سخت
تر است و مقاومت سایش بیشتری نسبت به فیلم های تک جرئی تشکیل شده از

دارد. ضریب اصطکاک فیلم

/Ti نسبت به گلوله های سرامیکی و فولادی در هوای مرطوب کمتر از 0.1 و در نیتروژن خشک، 0.05 است. وقتی این فیلم با فیلم های

معمولی مقایسه می شود، سختی ویکرز آن بزرگتر است و بنابراین کارایی
تریبولوژیکی آن بالاتر است. علاوه بر این، ویژگی های اصطکاکی این پوشش به
طور زیادی تحت تأثیر رطوبت قرار نمی گیرد و می توان از آن در کاربردهای
ماشین کاری خشک( مانند آسیاب کاری، دریل کاری، قالب های شکل دهی سرد و پانچ
های صنعتی) استفاده کرد.
در فعالیت های تحقیقاتی اخیر، تلاش ها در زمینه ی ساخت فیلم های نانو
کامپوزیتی خود روان سازی انجام شده است که از فازهای روان ساز جامد( به
صورت فاز گسسته و چند لایه) تشکیل شده اند. در این فیلم ها، مواد جامد
ر.وان ساز مانند

و

و یک ماده ی فلزی، سرامیکی سخت مانند نیترید یا کاربید فلزی مورد استفاده قرار می گیرد.
این پوشش ها می توانند با کندوپاش همزمان

و TiN یا TiB_2 تولید شوند. پوشش های ایجاد شده به این روش ممکن است شامل
نانو لایه های مجزا یا فازهای سرامیکی سخت و اجزای سولفیدی نرم باشد. سختی
این پوشش ها می تواند تا 20 GPa نیز برسد در حالی که ضرایب اصطکاک در این
پوشش ها در محیط هوای باز، حدودا 0.1 می باشد. به دلیل سختی بالا و اصطکاک
پایین، این پوشش ها را می تواند هم در کاربردهای ماشین کاری و هم کاربردهای
لغزشی مورد استفاده قرار گیرد. اخیرا، محققین پوشش های چند لایه از
MoS_x/Pb و MoS_x/Ti( با ضخامت لایه ای در گستره ی 4 تا 100 نانومتر) ایجاد
کردند. آنها این لایه ها را با استفاده از کندوپاش مگنترونی در دمای اتاق
تولید کرده اند. تست های سایش لغزشی در رطوبت 50 % نشان داده است که بهبود
قابل توجهی در عمر سایشی این پوشش ها نسبت به پوشش های MoS_x خالص ایجاد می
شود. طراحی سه بعدی پوشش های سازگار بر اساس ترکیبات چند جزئی

یا

منجر به بهبود ویژگی های تریبولوژیک در گستره ی وسیعی از محیط های مرطوب و
پارامترهای دیگر می شود. در حالی که پوشش های سخت TiC و DLC استحکام و
مقاومت به سایش خوبی دارند، DLC ها و

های روان ساز اصطکاک پایینی را در سطوح لغزشی ایجاد می کنند. ضرایب اصطکاک
این پوشش ها در هوای مرطوب برابر با 0.15 و در نیتروژن خشک برابر با 0.02
می باشد، بنابراین افزایش علاقه مندی به استفاده از این مواد در مکانیزم
های هوایی بیشتر شده است.
فیلم های نانو کامپوزیتی بر پایه ی

و

همچنین در سال های اخیر تولید شده است و قابلیت روان سازی و میزان تحمل
آنها در محیط های مختلف مورد ارزیابی قرار گرفته است. فیلم های کامپوزیتی
در طی تست های تریبولوژیکی بهتر از فیلم های تولید شده از

یا PbO و ZnO کار می کنند. علاوه بر این، این فیلم های کامپوزیتی از خود ویژگی های روان سازی خاصی ارائه می دهند.

در دمای اتاق خاصیت روان سازی ایجاد می کند. به هر حال، وقتی فیلم در محیط های اکسید و دماهای بالا قرار می گیرد، با تشکیل

، خود را وفق می دهد. این ترکیب در دماهای بالا اصطکاک کمی ایجاد می کند.
سایر مواد روان ساز لایه ای مانند گرافیت و HBN نیز در فصل مشترک لغزشی،
اصطکاک اندکی ایجاد می کند؛ اما آنها به طور گسترده به عنوان مواد
دیسپرسانت نانویی در پوشش ها مورد استفاده قرار نمی گیرد. برخلاف مواد روان
ساز سولفیدی، این مواد روان ساز جامد در محیط های مرطوب به خوبی کار می
کنند اما در شرایط تحت خشک و خلأ به خوبی کار نمی کنند. عموما این به طور
کامل پذیرفته شده است که هیچ جامدی نمی تواند اصطکاک و سایش اندک ایجاد
کند( صرفنظر از محیط و شرایط آزمایش). علاوه بر این، طول عمر بیشتر روان
سازهای جامد محدود است زیرا ضخامت لایه ی ایجاد شده از این مواد روان ساز
محدود است و به دلیل وجود محیط های خورنده، این لایه از بین می رود. عموما
هیچ روان سازی به تنهایی نمی تواند ضریب اصطکاک پایینی را در شرایط دمایی و
محیطی تست ها ایجاد کند. روان سازهای اشاره شده در بالا تحت تست های خاصی
به خوبی کار می کنند و تحت همه ی تست ها به خوبی کار نمی کنند.
مترجم: حبیب الله علیخانی
منبع: سایت راسخون